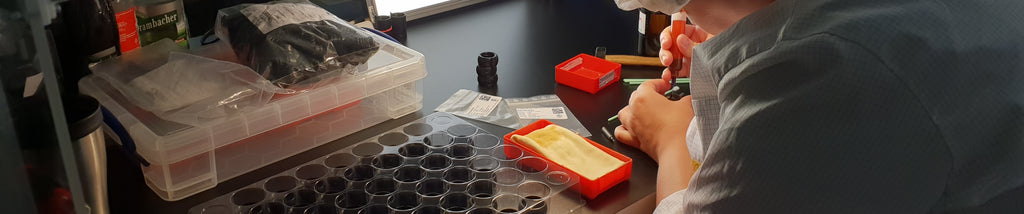
Steiner Optik Germany - Bayreuth factory visit
Steiner joined rifescope business rather recently, about 10 years ago. Very first 5-25 scope was made straight to fiercely competed military scope class, a elite league where product has to truly perform in all aspects.
Steiner had possibility to take sort of short-cut as existing military binocular manufacturer, but instant success was still somewhat big surprise to many- maybe even to Steiner themselves. More than likely such stunt could not have ended successfully without continuous optics production since 1947, particularly without decades of military-class binocular production and development. Steiner's best known products, 8x30 and 7x50 has been long time a standard binocular for many armies in the world - US Army included. All fundamental production segments such as development, manufacturing and testing were already available for product range expansion.
Note our normal disclaimer: As usually, we do apologize following article typos and even errors in advance. This too is written in rush between thousand other things going on and English is not our native language. Bear with us please.
Our MSR reticle was selected to be a option from beginning, so we had interesting possibility to see development long before scope line was published- even participate to certain small things. 5-25x56 scope was looking pretty good already full year before public release and production version finalization. Now, looking back 10 years afterwards, promising product has turned into solid alternative for any user- German Army KSK (Kommando Spezialkräfte) as latest example of organization selecting scope to their use for coming 338 Lapua G29 sniper rifle.
Steiner offered us possibility to visit their plant (click for 3D streetview) - and we also got permission to share information from bit deeper level than factory articles are usually. Following story is also pic heavy.
As a dealer of Steiner Military line, we know from first-hand experience that German-made M5Xi - scopes have exceptionally low failure rate percentage. It is not easy at all to achieve such reliability - especially without history with riflescope production. According to Steiner, key factor is quality: each and every part down to smallest screw is made in Germany.
Reliable basic design and solid construction is one thing - but final inspection and test procedures would still have to be done somehow different way. This made visit even more interesting. It was also interesting to have discussions about history and technological features- Steiner for instance still makes military binoculars with porro prisms while most of premium manufacturers have shifted to roof-prisms.
Hope you enjoy article!
Start of "Tour de Steiner". Lens and prism grinding machines. All lens machines had robotic feeders. Prism grinders on left, lenses on right.
One of very first steps with lenses. Gray racks are robot feeder trays.
Convex lens shape clearly visible.
Same room but other end. Half-parts of porro prisms about to start their next finalizing step. Prisms fixed temporarily into aluminum machining frames with UV- hardening glue.
Prism final polishing- although there was manual polisher and finalization step too in last stage. Prism racks spin and rotate. Prisms on top, pointing downwards. Lenses can be finalized very much similar looking way - except lens machine has additional axis for curved shape.
Prisms done!
Rack with finished prisms going into huge ultrasonic cleaner - a device sounding like doomsday machine. Any amount of impurity would cause lens coating to fail btw - meaning ruined lens or prism. This is not a cleanroom yet, but components are still thoroughly cleaned before proceeding.
Lens/prism production room final steps: inspection with various methods - and again some cleaning.
Visual inspection of lens against bright light - also various test machines in same area. Trained eye can catch many things: Cracks, unusual amount of micro-bubbles in glass, impurities, etc.
With this particular Kugler interferometer test machine, lens geometry and radius of curvature can be determined to an accuracy of +/- 1 µm. Equaling one thousand of millimeter or about +/- 0.00004 inch. Every self-respecting optics enthusiast should have one of these sitting in home we think.
Again some visual checking and cleaning. Lenses continue towards coating room. Latex gloves used to keep grease away from finalized glass.
Coating
Coating process details vary between manufacturers, but principle is always same. Small pellets or coating granules are inserted to vacuum chambers with non-coated lenses. Both granules and lenses are heated to 200-300C (400-600F). Gaseous state coating material sticks to lens surface permanently. High quality lenses have several coating layers, each with certain thickness to guarantee maximum transmission for desired wavelength area. Which is narrow, so several coating layers are required for highest performance lens. Main and original purpose of coatings is to boost light transmission, but it may be used for other reasons too. For instance, army optics have often anti-laser coating. Usually such coating harms image quality a bit, but its still better than fried eyeballs.
Probably the most secret place in any optics manufacturer: lens coating room. At this point we also had opportunity to ask questions. Like: "if human is inserted to coating chamber with adamantium pellets, will it he turn into Wolverine?" Answer was no.
Assembly
Laser range finder binocular laser alignment bench, this model under testing and adjustments. Two blurry spots (not that blurry in real life) show transmitted beam and electronic aiming mark in field of view. Sent beam and receiving lens must be aligned. As well as transmitted beam must be aligned to electronic aiming mark in field of view.
Permanently paired prisms forming double-porro prism for binocular barrel. First step in housing assembly is to mount it in binocular housing permanently - as in photo. Steiner uses in-house developed special glue for this, adding reliability and shock resistance.
As a small sidenote about binocular housings,
Synthetic housing material used in Steiner binoculars is called Makrolon, extremely durable synthetic material belonging in poly-carbonate family. This was mentioned few times during presentation. So we did some further research about this mystical material. Original Makrolon was invented in 1955 by German Bayern AG. Since then, many versions of original recipe has been developed by Bayern. One version is Makrolon published in 1967, developed with Steiner and used first time in new Bundeswehr binocular housings. New binocular concept was obvious success, US Army purchased huge amount of 7x50 (M22) binoculars too from Steiner in 1988. By the way -in early 80's, one version of Makrolon was used for CD:s, automotive industry and tactical gears are covered as well. Very first plastic headlight lenses are one version of Makrolon too.
Another thing Steiner is particularly proud are prims, optically most sensitive and also most important part of any binocular. Porro prism was invented and patented by Italian Ignazio Porro already in 1854, design was refined and used later by German Carl Zeiss too starting from 1890. Roof prism was first invented by French, and used 1897 in binoculars by Moritz Hensoldt in Germany. Steiner is still using this traditional porro prism design in their military line for few reasons: Porro is simpler, less sensitive with tolerances and does not require solving certain optical problems that are always present with roof prisms.
In practice it means that porro construction is possible to design impact resistant easier. Porro also has some natural optical advantages: naturally better light transmission as mirror prism surfaces are not needed. Porro reflects image internally and its efficiency can be very close to 100%. Roof prism loss of light is not much with latest di-electric coatings, but still- best coatings are always more expensive to produce and to include whole visible light spectrum with high reflectivity is diffucult. Unlike porro, roof prisms also require highest quality surface coatings to minimize or eliminate light beam phase shift, shift causing different light wavelengths (colors) to bend in different angles. This phase shift reduces both image contrast and resolution. Roof prism does not require solutions for either of above, but can not be made in narrow tubular housing as roof prisms.
All in all, due to fundamental principle of any porro binocular construction, porro prism binoculars are short and objective lenses are further apart from each other compared to typical roof prism binoculars. This width causes stronger 3-D effect- meaning better perception of observed image depth. Basically porro prism can also produce brighter image with same objective size- or, produce same image brighthess with smaller objective than roof prism.
Image below: Zeiss 8x30 military bino with Schmidt-Pechan -type roof prism vs Steiner Military LRF 8x30 porro prism laser range finder bino. Both are designed and bulit for military use, both have milliradian- based reticles inside.
Note difference in width, Steiner objectives are much further apart. This particular Zeiss is B/GA T*P* IF, multicoated lenses (T*) and phase-corrected prisms (P*), old but still pinnacle of Zeiss military binoculars as far as we know. Steiner housing is thicker due to room needed for porro prisms, but includes also laser for +6km / +4mile measurements and has bolt-in mount for tripod. Making bino appear much taller and bulkier "than it should". Note also black bluetooth module, Steiner supports Kestrel LiNK protocol.
Modern high-end roof prisms are optically excellent, but porro prism will always have certain principle advantages.
All in all, Steiner binocular is 900G shock proof, roughly double compared to big magnum rifle recoil peak. To demonstrate this, our host slammed set of binoculars on thick table in middle of conference room powerpoint exercise. Hard. I mean really, really hard. Did not dare to ask how many demonstrations one bino can take annually, but I checked bino quietly afterwards, image seemed perfectly fine.
Laser transmitter CB:s about to be installed into Makrolon binocular housings.
"Its like binocular but bigger!" 20x80 monster in collimation bench. In this point halves are aligned. Primary purpose for this product is border observation, airports and airspace monitoring. We also had opportunity to try these. Wide field of view stereoscopic image with big magnification is true pleasure to watch. Note little helper on top of tester frame.
Riflescopes
Military- line M5Xi riflescope eyepiece housing parts ready for assembly. Grabbed scope in same pic- open turret housing bottom is revealing elevation turret part that moves erector assembly up and down. This erector front-end horizontal and vertical movement shifts point of impact according to external adjustment turret position.
Inside cleanroom with white coats and hats on. Soon coming M7Xi 4-28 IFS scope with integrated display and ballistic computer in assembly table, some details blurred. Scope is not in serial production yet, but pre-production scopes are already made for testing and finalization. Scope is already available in our webshop as normal version and IFS version, reservations are accepted.
M5Xi or M7Xi riflescope erector ready for scope assembly, not sure which one this was. This part makes variable power riflescopes possible: tube has two moving lens inside. Lens positions are changed by rotating other end of tube: helix- shaped grooves change this rotation to longitudinal movement. First focal plane reticle lens with etched reticle is located on front part of erector. Erector also turns image 180 deg, as its name suggests.
Photo snapped from erector assembly machine screen- our MSR reticle again under construction. This machine aligns reticle lens on exactly right position during erector assembly. I could not take picture of machine itself, also all numerical info on screen is blurred. One can imagine lathe made in 2059 assembling optical capacitors for UFOs, it looked something like that to me. Steiner developed this machine in-house by the way, patents are pending.
Quality control room. But what is that green square object leaning against white cardboard box...?
Machine for resolution checking. Traditional resolution test chart can be checked with magnifier, test image located in apparent far distance for proper focusing. Did not ask it, but green background is probably used because 550nm green wavelenght is in middle of visible color spectrum. Wavelenght (=color) effects on practical resolution eye can see, shorter wavelenghts produce more visible resolution. For instance, resolution difference between violet and red is about 70%. Violet and red are in opposite ends of visible spectrum.
Test bench with mrad scale on wall, M5Xi 5-25 scope with MSR2 reticle under inspection. Big lens on front to scale full FOV for sheet on very close indoor wall.
Natural view for testing. Note horizontal stripe on painted brickwall, its actually test scale.
Heat + moisture cabinet for controlled envroment test. 80C/176F, RH100%. LCD screen showing 78C and dropping as door is open. Scopes and binos are moved between extreme heat, extreme cold and shaker machine during test. Cant remember for sure if freezer was set to -27C or -37C. (-17F or -35F).
Shaker between freezer and mini-sauna. Not so happy days for binoculars.
Shaker test sequence. Vibration amplitudes, frequencies and times will go trough according to programmed schedule. Test run is fully automatic.
Light transmission measurement room. This individual bino had 96.865% transmission peak on 570nm wavelenght.
Shock test machine, located in separated bunker-like room. Extremely noisy, sounding like pneumatic street drill. New M7Xi 4-28x56 stressed with 1000G impacts with split-second intervals. 1000G is roughly double compared to biggest magnums can produce in real life. Video has 2 slow motion parts.
Final inspection room, binocular under check this time. This friendly gentleman is one of guys who check products before final packaging. Part of procedure is seeing if binocular barrels are aligned exactly to same direction. Machine, as in pic, shows 2 crosses on screen. If they are perfectly overlapping, alignment is spot on.
If any further questions, feel free to comment in Facebook. More articles coming- stay tuned.
ali por
بسیار عالی هستن محصولات اشتاینرمن
چند نمونه از دوربینهای دوچشمی اشتاینر رو استفاددر اختیار دارم👍👍
علی پور
علیپور هستم از ایران.من چندین دوربین اشتاینر رو در اختیار دارم که تمامی اونها به خصوص مدلهای پرو از کیفیت بالایی برخوردار هستند و من لذت میبرم از تماشا کردن با انها👍👍👍
علی پور
علیپور هستم از ایران.من چندین دوربین اشتاینر رو در اختیار دارم که تمامی اونها به خصوص مدلهای پرو از کیفیت بالایی برخوردار هستند و من لذت میبرم از تماشا کردن با انها👍👍👍
ali por
بسیار عالی هستن محصولات اشتاینرمن
چند نمونه از دوربینهای دوچشمی اشتاینر رو استفاددر اختیار دارم👍👍
Reginaldo Barbosa Véras
Hello,
Please, i need know if the lens of my vintage STEINER BAYREUTH NACTHGLASS 7×50 binoculars is: coated, multicoated or fully coated?
Thank you.